Effective and efficient automation is only possible when the operational processes are first standardized and systemized, before moving to actual automation. As a part of Toyota Industrial Corporation, T-Hive’s automation tools are based on Toyota’s strong know-how in optimizing for productivity. This customer case shows how T-Hive’s Order Management System software forms a foundation for the customer’s automation.
About the Customer
The customer is a worldwide logistics operator who wants to standardize their material handling process in all of their sites globally. As with many logistic operators, the unpredictable nature of the business means the customer has not been able to use their vehicle resources in the most optimal way, despite careful plans and schedules. To become more efficient, they have a plan to introduce automation into their operations.
Business Challenge
Most of the (manual) logistic flows between different handling units on the customer’s sites are done by “push” operations, e.g. forklifts and trucks are dispatched based on a set schedule. But things don’t always go as planned, and when they don’t, the on-site operators need to improvise to solve immediate issues. The process planning becomes unpredictable, and the cueing of forklifts and trucks leads to unsafe and sub-optimal resource allocation.
To solve this issue, the customer needed to transition to “pull” operations, i.e. dispatching forklifts and trucks just in time, based on current needs. This would help the flow of transport units and materials become more stable and predictable, and the resources to be allocated optimally.
Toyota’s Know-How, Enhanced by T-Hive’s Smart Tools
Toyota Production System (TPS) principles are known to have helped optimize processes and increase flow efficiency in many TPS-driven factories. T-Hive, as part of the Toyota Industrial Corporation, uses that foundation to build the “brain” of the automation for our customers.
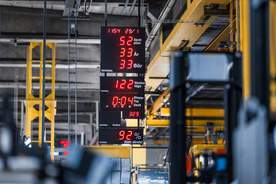
Example of TPS implemented in Toyota’s factories
From Principles to Practice
Our team analyzed the customer’s operational processes and built a simulation model that includes TAKT scheduling algorithms, according to TPS principles. With this tool, we could load real order profiles into the simulations and witness that applying TAKT as the basis for dispatching forklifts and trucks could help the customer transition to “pull” operations and even reduce the number of forklifts needed by an estimated 10%.
Based on this result, we made a proof of concept solution with T-Hive’s Order Management System software and tested it out in a real operational environment. The customer was satisfied with the test results, and we productized a final version of the software, ready for scaling at the customer’s multiple locations.
T-Hive Software as the Conductor for Automation
An advantage of T-Hive’s Order Management System is its ability to create workflows by building on blocks of individual task performed by each operator – a kind of visual programming. This could be tailored to any customer’s specific processes. It is relatively quick to build the right workflow steps in the Order Management System and implement them in real operations.
T-Hive’s Order Management System serves as the smart orchestrator, telling forklift and truck operators what to do and where to go at the right time for the most efficient operation. This order manager with the TPS logic is the “brain” of the automated system, the first step before any real automated vehicles can be introduced.
Taking containers out of and onto ships sounds like an easy task, but in total there are about 10 different workflow variants per use case. In practice, it means the Order Management System needs to be able to run more than 100 workflows, in all variants, in parallel, while making sure everything is orchestrated according to the optimized workflow. On top of that, the system also needs to be able to handle exceptions – equipment breakdowns, unexpected deviations in the location of the loads, and last-minute planning changes, to name a few.
Thanks to the flexibility of T-Hive’s Order Management System, we are able to adapt the software to fit the precise needs of these logistic operations.
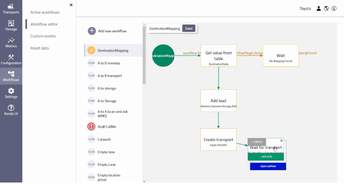
An example of workflow building in T-Hive Order Management System
Business Benefits
With TAKT scheduling deployed by T-Hive’s Order Management System, the customer can introduce pull operations into their work process with ease and precision, resulting in more efficient operations and reduction of resource usage (estimated 10% fewer vehicles needed). They have a strong basis for automation and will also be able to adjust workflows in the Order Management System easily to accommodate changing conditions.
The customer will use T-Hive’s Order Management System with TAKT scheduling on multiple sites and in due time introduce automation of forklifts and trucks.