About Kaufland
Kaufland is a German hypermarket chain, part of the Schwarz Gruppe which also owns Lidl. Today Kaufland operates over 1,500 stores in Germany, Croatia, the Czech Republic, Slovakia, Poland, Romania, Bulgaria, and Moldova. With an inventory averaging 30,000 items, Kaufland provides a diverse selection of food and goods for daily needs.
Efficient distribution centers are keys to Kaufland’s business. They have worked with Vanderlande for many years in bringing the best-performing automation system to their sites. Vanderlande has already equipped four Kaufland DCs in Germany and one in Poland with advanced automation technology. A sixth site in the Czech Republic is also under construction.
A New Distribution Center Equipped with New Technologies
The new DC at Geisenfeld, Germany, was to be equipped with a few new technologies: it is the first Kaufland DC to use Vanderlande’s next-generation automated case-picking solution STOREPICK to handle both incoming and outgoing goods; Kaufland’s award-winning new pallet design will be used in a fully automated system for the first time; and to transport those pallets, Vanderlande’s newly developed autonomous mobile robots (AMR) will be used.
Most importantly, this is the first warehouse operation where Vanderlande’s automated systems also control automated vehicles, and that is where T-FMS comes in.
Kaufland Klapp-Palette and the Chain Pallet Runner
One of the challenges for this project is to introduce the Kaufland Klapp-Palette (KKP) into a fully automated system. These are Kaufland’s innovative folding pallets designed to be better for transport capacity, environment, and the ergonomics of store employees. Unlike the standard Euro-pallets, KKPs are made from metal and have foldable side panels. The new pallet specs required new custom-designed autonomous vehicles to transport them safely and efficiently.
As a result, Vanderlande’s autonomous mobile robots (AMR), the Chain Pallet Runners (CPR), are created to carry these pallets, and they are controlled by T-FMS.
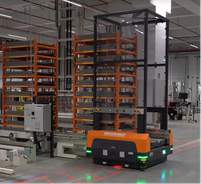
Stacks of empty Kaufland Klapp-Palettes being handled by a Chain Pallet Runner
T-Hive Fleet Management System
T-Hive Fleet Management System controls how an automated vehicle should move and what tasks it needs to complete. The smart algorithm picks the most efficient route for each vehicle, maximizing throughputs while preventing collisions and deadlocks.
In this Kaufland DC, T-FMS controls 16 Chain Pallet Runners on two floors of the DC:
- 14 CPR vehicles on the ground floor, transporting pallets in 3 different flows at a rate of 240 pallets per hour.
- 2 CPR vehicles on the first floor, in a very narrow environment for empty pallet replenishment.
On an average day, T-FMS handles 1500 pallets, in a 24/7 production environment.
New Challenges Bring New Capabilities
The Kaufland project comes with a few technical challenges, so we used the opportunity to improve T-FMS further.
Integration
The main technical challenges for T-FMS in this project were to integrate the newly developed CPR vehicles (using VDA 5050 protocol) and to seamlessly integrate T-FMS with the Vanderlande warehouse management system, with T-FMS running in a Kubernetes environment for the first time.
New Features for Dynamic Warehouse Environment
DC operations are dynamic in nature. With human operators and a lot of equipment involved, the environment is not always controllable – a challenge for automated vehicles. The automated system needs to be robust enough to carry out 24/7 operations despite unexpected occasional disruptions.
To maintain the high throughput in such a dynamic environment, we designed new features for T-FMS, including:
- AGV recirculation when loaders or unloaders are temporarily blocked
- Resending vehicle commands automatically when disrupted by weak Wi-Fi spots
- Driving around delayed or faulty AGVs, avoiding “traffic jams” and deadlocks
- Quick recovery if T-FMS shuts down unexpectedly
- Quick and easy insertion and removal of AGVs to the system, in case an AGV has problems and needs to be taken off for fixing
- Real-time visualization for improved monitoring and diagnostic capabilities
These features are valuable not only for Kaufland, but also for the subsequent projects that T-FMS is involved.
Better Data Visibilities with DataCollector
We also integrated T-FMS with T-Hive DataCollector so that all the information collected by T-FMS can be stored and displayed in real-time, in meaningful charts and tables. With DataCollector, both the engineers and the customers can see clearly whether the vehicles are performing up to expectations, where an issue occurs, and the possible causes. This helps to make sure the automated system can continue operating, and that the business of Kaufland is not disrupted by an issue with the autonomous vehicles.
Business Benefits
Kaufland has always been investing in logistics innovation to stay competitive in the food retail market that is exponentially growing. T-FMS takes Kaufland’s innovation further by automating the transportation of their newly designed pallets and allowing them to be transferred quickly even in very narrow aisles, making the operation more efficient. DataCollector enhances the system monitoring to avoid serious disruptions to the operations.
With Vanderlande automated solution, productivity and profitability at the Geisenfeld DC is expected to increase significantly, and a big part of that is possible thanks to T-Hive solutions.