Our Progress in 2024
With the end goal of having autonomous airport tuggers delivering baggage to and from aircraft at the Schiphol Airport, we started by designing the system and running simulations of all airport apron operation scenarios with the autonomous vehicles, before deploying the system in real life.
Realistic Emulation
In order to have a better understanding of the operation, we use T-Suite to emulate the outdoor operation with the autonomous vehicle.
Since our last emulation demo, much progress has been made in the T-Suite to allow for a more realistic emulation. We are now able to build the airport apron layout in the Digital Twin and import it into Order Manager and T-FMS. The truck trailers are also now emulated (although not yet shown in the visualization.)
How does the emulation work?
First, we use Digital Twin to generate the airport layout. With the smart features of the Digital Twin, we can easily design the system layout based on the real environment and required operational conditions. When satisfied, we export the layout into the runtime stack part of T-Suite. (Later on, if we need to modify the layout, we can also go back to the Digital Twin and easily do so.)
With the layout in hand, the Fleet Management System receives orders from Order Manager and instructs the vehicle on where to go and which tasks to perform. For this emulation, we use an emulated vehicle created by Vanderlande’s CARE (CApacity Realistic Emulation) that very closely mimics the characteristics of real vehicles. The emulation is visualized through FleetTracker, our 3D visualization tool.
The diagram below describes the emulation stack as it currently stands. T-Hive develops the components in yellow, and those are what you will see in this demonstration.
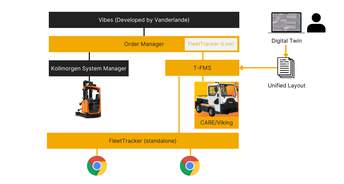
At the top of the stack is Order Manager, which is the order management system that not only processes orders from external sources but also manages the site location configuration and the process workflow for every use case. During the demo, we will use the “CallMeScreen” with a simple UI button to mimic order creation by airport operators.
Once the order is processed and the vehicle is instructed to drive, T-FMS will be working as part of the stack. With the latest development, T-FMS now supports vehicles with trailers. That means this emulation will be more realistic with all the trailer behaviours taken into account.
T-FMS has the information of the vehicles registered on site. For apron operations, there will be many manual operations that the autonomous vehicle has to “wait” for; for example, the manual loading and unloading of baggage containers (ULD). Our current T-FMS supports multiple “wait” actions – a new feature that allows autonomous vehicles to work smoothly in a mixed system that includes human operators.
As for the vehicle, we have implemented the Simai TE152 truck in the “CARE” emulator. The emulated vehicle has been created to behave as close to the real vehicle as possible. The goal is to be able to run the real vehicle with the same software setting by easily swapping the emulator out for the real vehicle.
Last but not least, T-Hive’s visualization tool “Live” (powered by our FleetTracker software) allows you to see the 3D visualization of the emulated system. With this tool, we can import customized 3D objects in .gltf format. The result is a 3D “animation” that shows you exactly how the real vehicles will run in real operations at Schiphol Airside.
In this demo video, we demonstrate the function of T-Suite and create orders just like in real operations.
Note: we are still working on the visualization of trailers, so in the video you will only see the tugger running without trailers, but you can be sure that the trailers are emulated and are there, just not visible to the naked eye!
From Screen to Reality: Small-Scale Physical Demo
Seeing is believing, and we believe seeing physical things creates better understanding than just digital models. Between the emulation and real airport tuggers, we have used the T-Suite and a modified small Kollmorgen vehicle to create a small-scale physical demo to show how the autonomous vehicle will work with humans in real operations.
This demo uses the same software suite that we use in the emulation, and will use in the real operation, but connecting it to a small forklift disguised as a miniature airport towing truck, fully equipped with baggage ULD trailer. From our test site at Toyota Material Handling head office in the Netherlands, you will get a feel for how the ULD replenishment use case would look at the Schiphol platform.
Watch the first video at the top of this page.
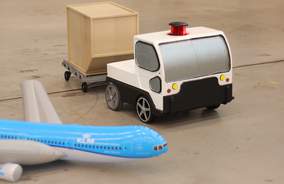
A lot of new developments with cutting-edge technologies going on behind this project. We are excited to see these autonomous airport towing trucks driving in Schiphol in the near future!
About BrightSky
The BrightSky project is an open partnership that aims to stimulate intensive and long-term collaboration with, and innovation at, many companies in the aviation sector. BrightSky is therefore a fertile breeding ground for R&D within and outside the aviation sector in general. BrightSky aims to allow Dutch aviation to play a leading role in Europe for a long time and to prepare itself to take advantage of new economic opportunities.
Through this project, the consortium partners want to focus on innovation as a means to accelerate and strengthen the position of the Dutch aviation sector at and around the airport.
BrightSky Mobility Fund
The BrightSky partners have selected topics for the grant application that fit in with the R&D Mobility Regulation and are complementary to other initiatives in which the various partners are already involved.
The R&D Mobility Regulation project BrightSky consists of 5 work packages. Within these work packages, BrightSky emphasizes the following three integral aspects:
- Social innovation – how do we obtain a healthy workforce where, with the right direction, we can develop talents in the direction demanded by technological developments and which meet the challenges presented by the market?
- Digitization – how do we use the opportunities that the innovative possibilities of digitization (storage, work content, scanning, data sharing and preventive maintenance) offer us?
- Sustainability – how do we approach the subject of sustainability (labour potential, ecosystem development, economic and environmental impact)? How do the work packages contribute to the sustainability goals for 2030?
Smart Autonomous Airside
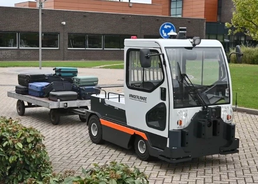
BrightSky Airport Vehicle
T-Hive and Vanderlande are involved in BrightSky’s Work Package 3 (WP3 – Smart Autonomous Airside) which aims to develop an airport system that systematically makes the coordination and control of airport sub-systems more sustainable and digitised, including the autonomous handling of baggage to and from the aircraft.
Two main tasks have been defined.
- Defining, specifying, developing and validating the tactical prioritisation for multi-fleet logistics and its governance system. The end result will consist of a detailed process description – including a flowchart and a system definition – of how to arrive at the most optimal selected prioritisation based on defined KPIs.
- Defining, specifying, developing and validating the control of a secure automated baggage handling process. The end result will consist of an emulation environment in which operational scenarios can be simulated and visualised in such a way that a realistic picture is obtained of relevant processes and systems. In this way, the system control is (at least in part) realised by its control components. However, other elements from reality are replaced by models or simulated components.